3DCS Tolerance Analysis
If you want to get very high quality products, we need to use the 3DCS Variation Analyst to help me to improve the out over tolerance risk, can ensure the each assembled product meets the cosmetics and use requirements, according to this idea, maybe we can increase the tolerance requirements to solve these issues, right? No, we know it is a very high cost of high precision component, then which tolerance value is beneficial, I want a low tolerance and high quality assembled products, and the 3DCS Variation Analyst can offer this analysis.
Mold Design:
PRODUCT DESIGN & DEVELOPMENT:
Using 3D design software, we will transform your product ideas into reality. Our experience in the design, development, and manufacturing of custom injection molds and support tooling provide the expertise needed to solve any product challenges. We welcome the opportunity for early vendor involvement during the conception stages of your project, then we offer some new proposals about simplify the tooling structure to reducing cost and time to market.
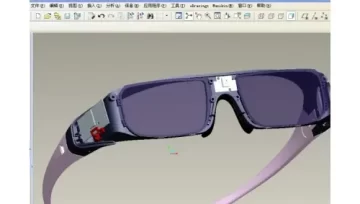
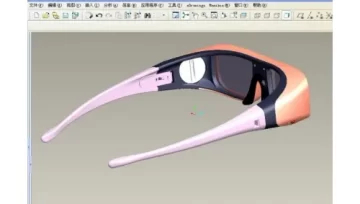
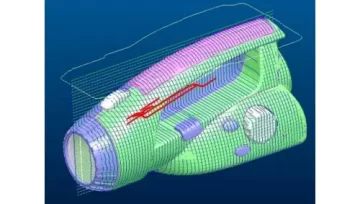
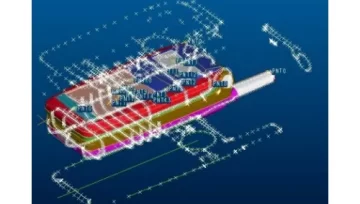
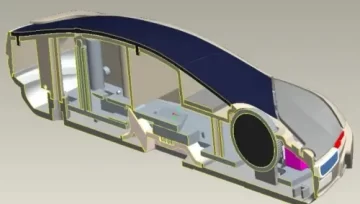
2D&3D Mold Design
Understanding advanced mold-making processes and technologies, we utilize the latest CAD/CAM tools to transform our customer’s concepts into viable finished products. will communicate with you quickly and effectively to accommodate all mold design modifications or revisions.
Our design /engineering technologies include:
• AutoCAD(2D layout)
• Creo/SolidWorks/ZW3D/ Unigraphics NX(3D Modeling)
• Unigraphics NX/ZW3D (CNC Programming)
• MoldFlow Plastics Insight/ Moldex3D(Plastic flow/warpage simulation)
For the provided 3D part model, we will review clearly and make feasibility report and feedback to customers for any problems we found.
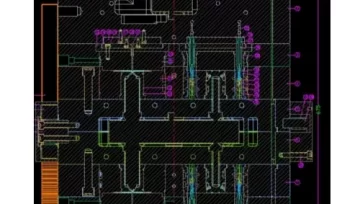
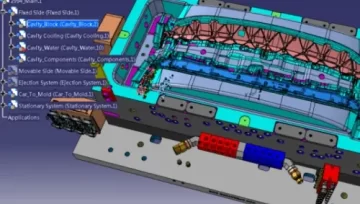
Design For Manufacturing (DFM) and Mold Flow Analysis
Design for manufacturing (DFM) evaluation occurs both internally as well as with customers, proposal of part design optimization, injection molding options are present by HKY-Technik design team and discussed with customers to decide the best solution to meet production demand, we provide the customer with feasibility report for part design optimization before mold design, The DFM procedure can help to avoid unnecessary mold modifications and extra cost and time at later stage.
Use the Mold flow softwave to analysis can figure out molding and cosmetic risks that may exist in advance, like location of the weld line, warpage, insights of how to improve the cooling efficiency and shorten the injection molding cycle time as much as possible, and the part prerepair deformation floow the warpage value by moldflow analysis .
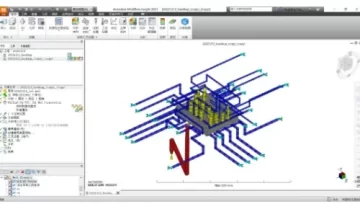
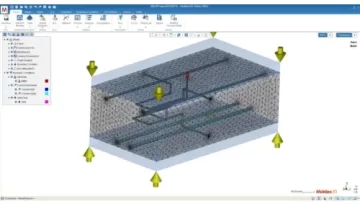
Manufacturing
Technology:
determinate the cost economy of the manufacturing process
looking for optimum production steps from the point of view of highest quality
CNC Machining:
CNC machining is done on machine as possible as we can
Copper & graphite electrodes.
programs are generated in Unigraphics NX
EDM Machining:
uses precise copper electrodes made of highest quality material
Check every electrodes dimension by CMM before EDM
Can do texture by EDM machine directly.
3 Axis work together from different direction.
Polishing:
we are capable of polishing complicated surfaces to briliant polish (glass surface)
fully equipped welding workplace
Moulds Testing:
sampling and tests are carried out on modern presses of the HAITIAN brands
the test curves are ordinarily documented in the test protocol
the aim of the tests is to give the customer a mould that has been tuned and debugged
properly both from the technology and dimensional point of view
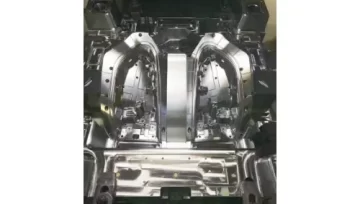
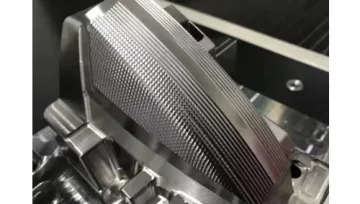
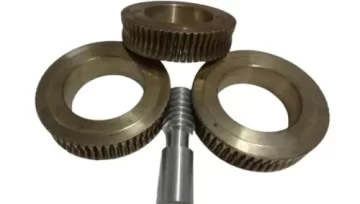
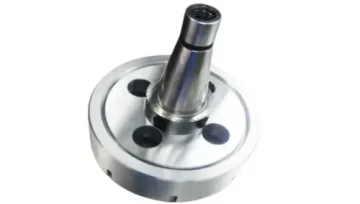
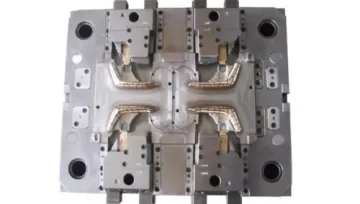
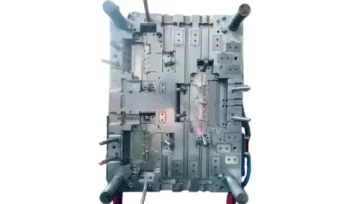
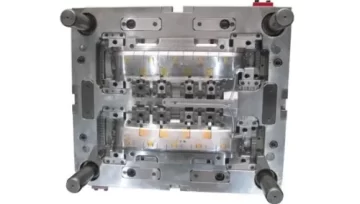
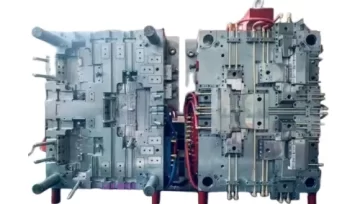
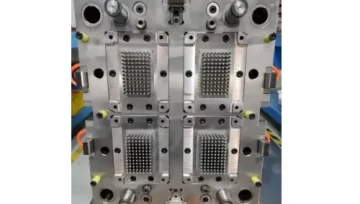
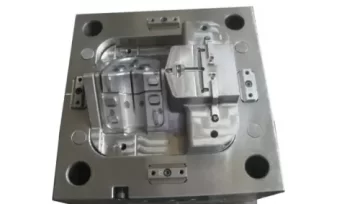
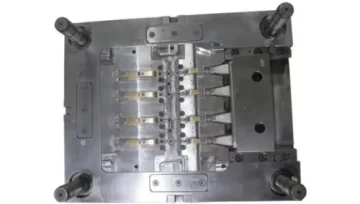
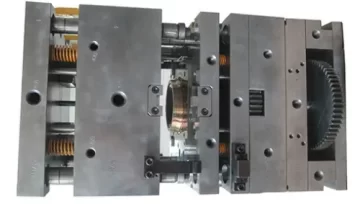
INJECTION MOLDING
We can offer the best injection moulded part for you, we can moulding the less-than 0.1mm of part PC V0, and greater than 70mm of PMMA part.
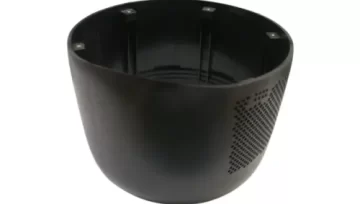
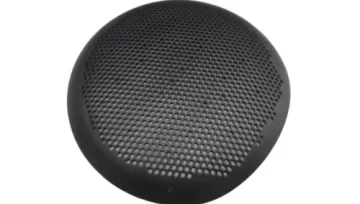
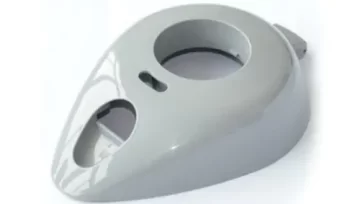
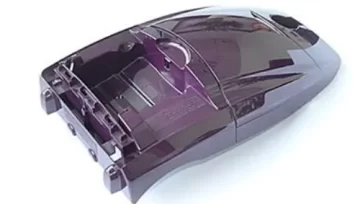
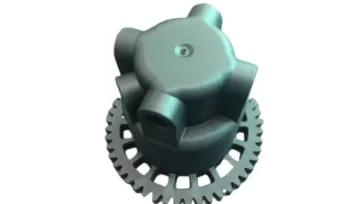
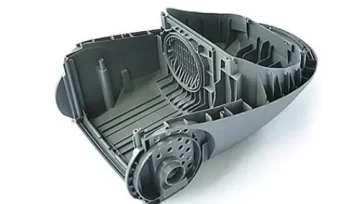
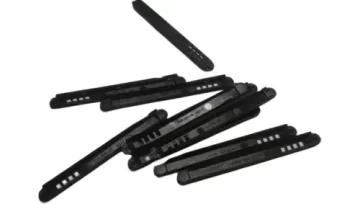
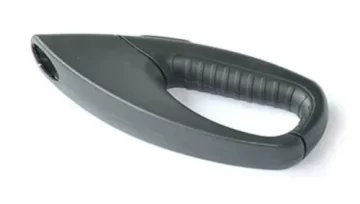
SECONDARY PROCESS AND ASSEMBLY
We help our clients to manage secondary process includes oil painting, silk printing, lasering, electroplating, wrap fabric and assembly, from design to final product, our one stop service help you to avoid dealing with too many unverified resources at the same time, and minimize risk of quality issue.
Electroplating
Electroplating is the process of using electrodeposition to coat an object in a layer of metal, The purpose of electroplating.
1. Corrosion protection 2. Protective decoration 3. Wear resistance 4. Electrical properties: According to the working requirements of the parts, provide coatings with conductive or insulating properties.
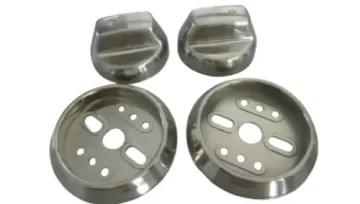
silk-screenings
silk-screening is a highly specialized process used to print on flat and flexible plastic surfaces.
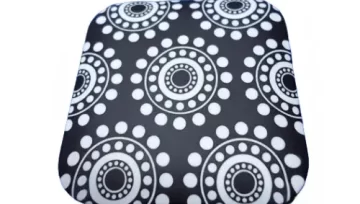
Laser Marking and Engraving Plastics
Similar to screen printing and pad printing, it can print words or patterns on plastic products. But in contrast, laser marking has the advantages of faster marking speed, more beautiful image marking, higher resolution, never wear, and strong anti-counterfeiting.
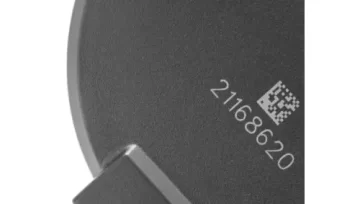
Ultrasonic Welding
For ultrasonic welding, sound waves with a high frequency are used. The sound waves are introduced into the plastics and cause them to heat up. Plastic welding using ultrasonics has many advantages over adhesive or conventional welding methods: It saves energy, is highly precise, requires no other tools or materials and is cost efficient. You also achieve precise and reproducible weld joints which don’t require further processing.
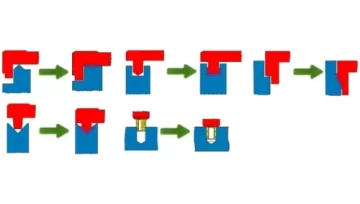
Heat pressing to wrap fabric with plastic cover
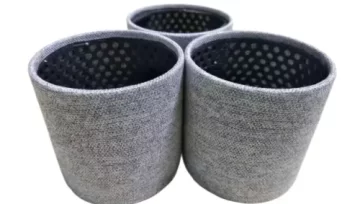
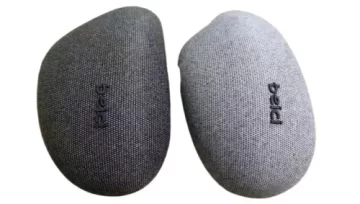
PROJECT MANAGEMENT
•Detailed planning:
•Weekly report with mold making photos or vedios
•Mold trial report
•Mold trial video
•injection parameter
•FAI report
•Production inspection report
•injection mold check list
Objective:
•Ensure injection molds & molded parts we deliver exceed the expectation of our customers.
•On time delivery
•Efficient communication to bridge the gap between customer and manufacturing site.
•Enjoyable working relationship